Apprentices playing their part at PP Control and Automation
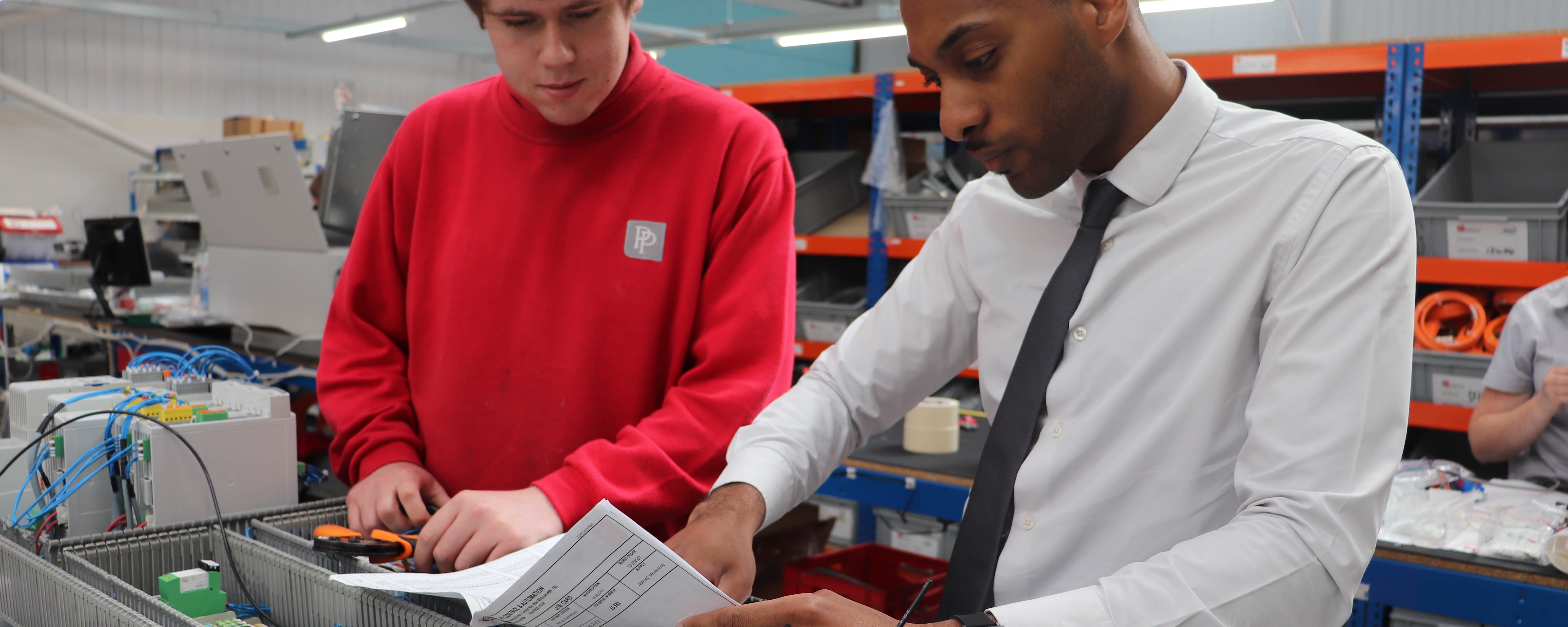
With a number of apprentices joining PP Control and Automation year on year, the electronics manufacturer is taking pride in the robust training and development plan put in place for each individual. It is a plan that has seen apprentices progressing onto higher level qualifications and enjoying more responsibilities.
The company also expects to see more apprentices work their way up to senior engineer roles in future.
Different skills sets
“What we do here is unique,” said Scott Ward, Continuous Improvement and Training Coordinator. “As we get to know our apprentices, we identify different skills sets, tailoring their training and development to bring out the best in them. We do this by encouraging them to work on the shop floor, main assembly, in purchasing and continuous improvement.
“There’s definitely a ‘grow your own’ structure in place. We’re also taking people into the operational side of the business – HR, finance etc. If someone is showing an interest in certain roles, we can help them pursue these with the right practical and personal support.”
Adapting to Covid
While the Covid pandemic has impacted heavily on the business operations of many organisations and resulted in some company’s putting their apprentices’ training on hold, PP Control and Automation has been able to adapt and find new ways of working.
Sanitisation machines have been produced for ProtectPod. The company has also been contributing to the design and error proofing processes for the manufacture of ventilations for NHS Nightingale Hospitals. Production engineer and former apprentice, Marcus Wesson was one of the team supporting the assembly side project.
Through their partnership with McLaren, the business has been able to support the supply of cable harnessing that was used in over 10,000 units. Marcus with his understanding of engineering and manufacturing experience was able to support in the practicality of getting the design into rapid manufacture. This meant that their manufacturing teams were able to produce and test hundreds of cable assemblies each day.
Lockdown learning
Learning has continued throughout lockdown for all company apprentices.
“Walsall College’s learning approach has worked very well for us,” continued Scott. “The apprentices have attended online lectures together while on site or studied from home. No-one’s learning has been put on hold.”
Scott works closely with Walsall College’s apprenticeship delivery team to ensure that a broad range of practical skills are delivered through the Level 2 and 3 engineering technician apprenticeship standards.
When aspects of the apprenticeship standard refer to traditional engineering manufacturing principles that are less relevant to PP Control and Automation, the college ensures that the company’s apprentices are still gaining knowledge and skills that benefit the business while meeting their qualification requirements.
Scott explains: “Some of the equipment the college uses such as machine turning and milling aren’t used here. However the apprentices still work with these in order to understand manufacturing processes that work across all businesses. Not only are they finding out what makes these processes work, they’re understanding the importance of getting these processes right every single time, as well as the impact that errors can cause.”
Scott and the college team also ensure they are in close contact. This is through joint review sessions for the apprentices and regular cross site meetings/visits.
Scott added: “Apprentices are seen to be at the heart of the business. A rolling programme is in place. We’re keen to take our internal development plan to a point where someone joins as a school leaver and works their way up to a senior engineer position.”
“As PP now look forward towards 2021, we are planning double digit figure growth for this year, with plenty of new opportunities that our apprentices will sure to be playing a part in within the coming months.”